December 2024
The elegance of Rolex watch dials is not a mere detail: behind an attractive design, there hides a mastery that is invisible to the eye, but palpable in its usability, durability and reliability.
And it’s not by chance that it is called an art: in a compromise between traditional craftsmanship and cutting-edge technology, the creation of a dial has an alchemy unique in its kind. It's no wonder that they are the business card of any watch, the cover that denounces quality, the target of the first glance, the geometry that announces the brand, the stage where it is printed in small letters - but much larger than its font. size - “ROLEX”. “We often say that the dial is the face of the watch, because it is what will give personality to a given model,” explains David Riboli, in charge of watch prototypes at Rolex and responsible for transforming designers' sketches into dial prototypes. “This is an even more real dimension when it comes to a dial made of natural stone or nacre, because in this case, each dial is literally unique. The dial is therefore a key part of the watch’s exterior, which is born from a rich and intense dialogue between designers and research and development teams.”
It is not just because of its central positioning that the dial steals all the attention: its shape is highlighted by the importance of its functions. Of course, it must be aesthetically pleasing - after all, it is the most visible and decorated area of the watch -, but its metal screen has a purpose: it is used, of course, to display the time, among other tasks, so it must also allow reading clear and easy time. This disc with a refined finish, which reveals the entire personality of the person wearing the watch, finds the Swiss brand a master in this matter, as the maison is capable of conceiving and producing this emblematic piece as a whole. This detail in the manufacture of a dial is an important strategic asset for Rolex. So much so that the brand has a production unit located in Chêne-Bourg, Geneva, where around 500 people work just to manufacture the dials. From the most traditional gesture to the high-tech machine specially developed by the brand, all operations are perfectly executed, systematically controlled and evaluated at regular periods to permanently increase the level of final quality, which implies permanent collaboration between the designers and engineers involved. in the development of a dial - and its consequent creative freedom and strong innovation dynamics - which are a decisive advantage, among others, for the Swiss house. Mastery does not mean, however, that there are no impasses or limitations: “By definition, the creation of new dials is not a path made exclusively of successes and achievements”, demystifies Riboli. But it's what you do with these obstacles that sets the maison apart. “We have an infrastructure and resources that allow us to go particularly far in our activities. (…) Furthermore, we keep the technologies we use constantly evolving. Therefore, there are always new possibilities to be tested, innovative concepts to be tried. For example, we were able to compose a motif with small flowers combining the traditional sunray effect with laser engravings. This allowed the petals to be worked with a sunray, matte or grainy texture, and to create a subtle play of reflections that gives the dial its personality. Finally, in the center of each flower, a hand-set diamond shines.” It is no wonder, then, that the process is called “art.”
Under the protection of the case, but also fully exposed under the sapphire crystal, the dial allows the house's designers to explore unusual paths and opens the door to multiple experiments, such as playing with colors, motifs, materials, finishing and decoration methods. and, of course, graphic design. “The design of a dial, no matter how flat and round it may be, literally requires us to change the way we see things”, reveals the expert. “It also requires that we know how to listen, because the invention of a new display is, above all, a matter of dialogue, exchange and even debate. You need to be able to understand concepts such as the depth of a color, the structure of a surface, the regularity of a motif, to give an example, the striations of a sunray finish. But that's not all. It is also necessary to consider the context in which the dial will be placed: the shade of the case and bracelet, the appearance of the bezel or even the depth at which the dial will be installed in the case. Sometimes, my colleagues and I also play the role of obstacles, because it is not always possible to achieve what our imagination suggests, even if we work tirelessly to do so.” But the team always tries to turn things around to move from sketch to reality in the most creative way possible. And always keeping in mind the history and identity of the model in question and the brand.
Creative freedom has, of course, also constraints that are linked to basic quality criteria, a prerogative of the name that protects the pieces: for example, like all components of the watch, the dial is also subject to impacts, which is why its Resistance is thoroughly assessed throughout the entire process to ensure that all elements attached to the surface of the dial remain in place under the watch's predictable usage conditions. It's not the only quality test, of course: from cutting the base metal disc to final inspection, the various steps follow a strictly designed scheme to ensure there are no defects. And, taking into account that the well-trained human eye can detect imperfections on the order of a tenth of a millimeter (the thickness of a human hair), the challenge is not lacking. And that's why the brand leaves nothing to chance, specializing a list of artisans in this art to ensure that it remains at the forefront of this aspect. With the necessary know-how and knowledge acquired over time, without turning a blind eye to innovation to constantly push the limits of this area, Rolex has numerous experts on its staff: from mechanics to crimpers, from galvanizers to dial specialists. , including the enameler, the engineer specialized in PVD techniques and the operator specialized in carrying out finishes such as sunray, the multiplication of professionals in each task is a mirror of the value that the name watchmaker attributes to this variable in its watches. Over the years, these artisans have refined their knowledge and passed it on to new generations who have adapted it to the evolution of dials: the DNA is maintained, but grows with today's demands, translated, for example, into technical improvements (which also arose for aesthetic reasons). Another important variable to be taken into consideration in this art is resistance to ultraviolet rays: prolonged exposure to these rays can effectively change the color of a dial and the elements that make it up, and this is precisely why Rolex carries out aging tests during the research and development phase, during which dial prototypes are subjected, for long periods, to different types of sunlight.
But apart from the pragmatic factors of dial design, there is the design factor that is never neglected. This process often begins unexpectedly following instructions from the General Directorate: the designer then makes the first sketches, does research and studies new ways to respond to the request. The objective is to create an appealing display that triggers emotions and captures curiosity and then dazzles with its details. After this stage, there is a fruitful exchange with employees from the Research & Development Division responsible for preparing the displays, which translates the designers' proposals into prototypes, in an alliance between aesthetic exploration and technical development. In this intersection of expertise, new ideas are generated, resulting from the use of technologies and know-how linked directly or indirectly to the manufacture of displays, in what is an exchange with added value for both parties and an important stimulus for innovation. To such an extent that Rolex has already registered several patent applications in this area, for example, in terms of surface treatments, manufacturing of appliqués or morphology of the base plate. Every year, several hundred dial prototypes are developed, but only a few will be produced and become part of the brand's catalogue: those that have gone through a strict and rigorous selection process, on an aesthetic and technical level, but also on a commercial level.
More than 60 operations are required to transform a metal disc into a finished dial ready to be mounted on the clock, the first of which is the sketches for the round plates cut from a strip of brass (easy to work with, it is appreciated for its qualities mechanics and for its conductivity, but also for its malleability, an essential property for dials set with precious stones or enameled) or gold. If the dial is to include a date or day window, this is done by stamping and then the holes that serve to attach the appliqués are drilled (the smallest ones measure just 0.2 mm in diameter). Polishing followed by sandblasting makes the surface uniform and eliminates any machine finishing marks. The brass dials are dipped in a galvanic gold bath and, subsequently, in a nickel bath, in order to create a fundamental protective screen that prevents oxidation and guarantees the homogeneity and longevity of the color that will be applied, and can also be subjected to a silver bath, if you want to give a sunray finish. Gold dials, since gold does not oxidize, are not subjected to these treatments. Then, the aesthetic and decorative details, if applicable: whether coloring, in the case of lacquered dials, or adding precious stones, Rolex has a vast palette of finishes to beautify its dials, the most traditional being sunray (highlights small striations that run from the center to the outside of the surface obtained by the movement of two brushes that sweep the dial coated with a slightly abrasive solution). But it also has a fine satin finish (with sandblasting, it creates a uniformly matte surface) and other watchmaking decorations, from the most traditional, such as guillochage or grand feu enameling, according to the champlevé technique, to the more contemporary (executed by laser, a medium that allows the creation of different types of structures, such as granulation). In the case of adornments, the special attention to the quality of resources, a hallmark of the brand, has gained loyal customers: opal, onyx, falcon's eye, turquoise, green aventurine, carnelian, eisenkiesel or even nacre and meteorite, to name just a few, are materials with unique colors and appearance, selected after research across the planet carried out by the maison's teams, who even visit the mines and production sites. The richness of structures and tones is infinite, allowing the brand's catalog to be constantly enlivened by dials that are always precious and unique, even due to the artisanal work they contain: certain exquisite watches boast a dial partially or completely set in diamonds, with several hundred Hand-set precious stones, one by one, on an 18-karat gold base plate. Sometimes it is just the hour markers that are decorated with diamonds or simply made from a single precious stone.
In the case of coloring, it is obtained thanks to three different techniques: lacquer (used mainly for deep colors such as black, white, pink, turquoise or green), the application of the lacquer is done with an airbrush in thin layers in a clean room to ensure the absence of dust particles; once all layers are applied, it is coated with a clear varnish and finally the dial is polished to add more shine); electroplating (for metallic colors, through this electrochemical process, the dials are colored in electrolytic baths in which thin layers are deposited by the effect of an electric current that attracts and fixes the metallic ions suspended in the liquid on the dial); and PVD treatment (through the deposit of ultra-thin coatings of oxides, metal alloys or nitrates, in the form of layers of atoms less than one micron thick), Rolex played a pioneering role in the development and integration of the production of this technology , complex and delicate, which allows you to create countless different colors). Dials colored using electroplating or using the PVD technique are coated with a transparent finishing varnish, called zapon, which gives depth, shine or a matte appearance, protecting the surface of the dial. At the end of the process (before assembling the watch face), the different inscriptions and sometimes also the hour markers are created using pad printing, a technique designed to print the desired texts and symbols, which also allows the creation of inscriptions with volume, repeating the operation several times. At every stage, execution requires excellent dexterity for a result that does not fall short of perfection - one that can always be refined and multiplied, as the house has done over the years, never stopping to learn to improve what can be improved, even if it is in terms of choice (of colors, for example) or streamlining process.
When finished, the dials are transported to the brand’s Acacias facility in Geneva, where the final assembly of the watches takes place. The objective of the final piece is to ensure that the customer “feels pleasure and desire when looking at the dial of their watch, which will have to stand out naturally for its beauty and harmony”, shares David Riboli. “You must seduce by the perfection of your design, your color or colors of your decoration. To achieve this objective, we need to exercise our eyes and our ability to observe. This is also one of the great qualities of the majority of employees who work on the design and manufacture of the dials. Of course, there are measuring instruments, such as the spectrocolorimeter, which evaluates the tone of a given color. However, nothing replaces the experienced human eye. This is why, for example, all sunray dials are examined one by one to ensure the harmony and regularity of the striations. A dial seduces with its beauty. It must, therefore, be manufactured with perfection”, concludes the expert, in a message that is simple: in this disc of colors and reflections that make the watch shine, art, history, know-how and technology are combined in a talented way, in the which is a confirmation of Rolex's consummate mastery in the creation and manufacture of that element as strategic as it is symbolic - the dial.
Translated from the original in the Jewellery Supplement "Spoil me", published December 2024 with the What's Next issue. Full credits and stories in the print issue.
Most popular
.jpg)
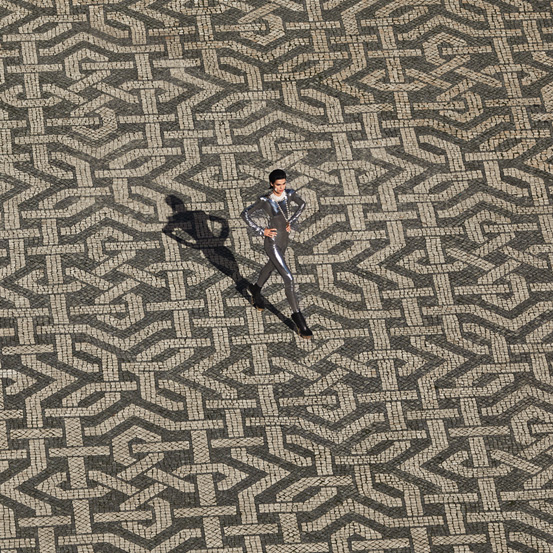
Relacionados
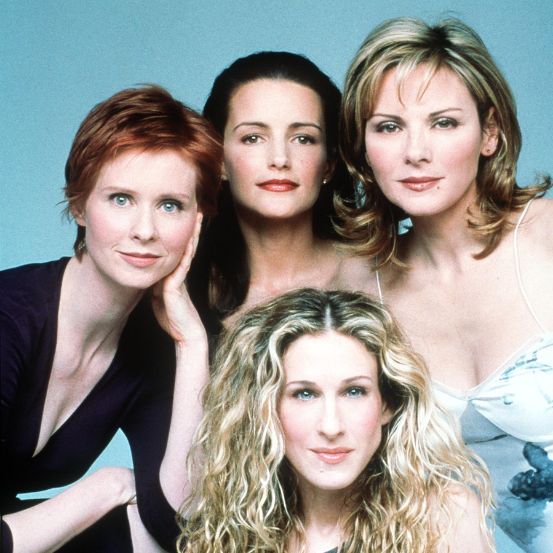
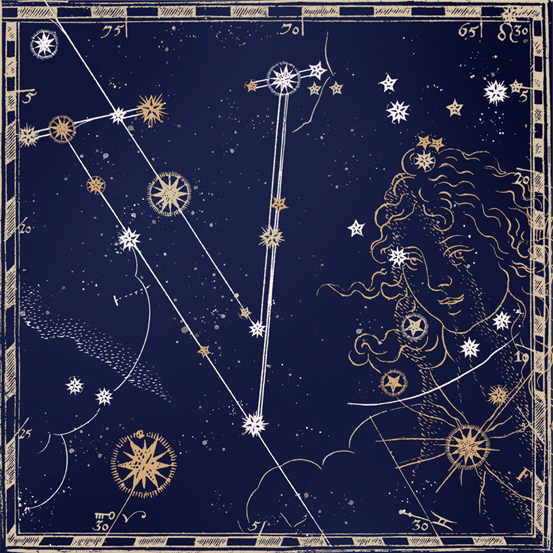
.jpg)
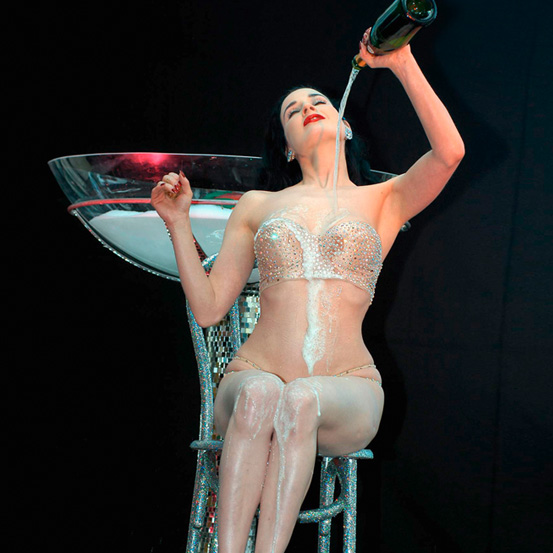