“I love that sweater!”, a 30-something woman exclaims, clearly excited about her friend’s new outfit. “Chanel. Organic Cotton. Made in Paris. And yours? It’s beautiful.” The answer was quick: “Thank you! Pineapple leather. Made in a lab.” Creativity connected to technology to the service of Fashion has brought materials and novelty so out of the box that they’ll forever change the chitchat between bff’s.
“I love that sweater!”, a 30-something woman exclaims, clearly excited about her friend’s new outfit. “Chanel. Organic Cotton. Made in Paris. And yours? It’s beautiful.” The answer was quick: “Thank you! Pineapple leather. Made in a lab.” Creativity connected to technology to the service of Fashion has brought materials and novelty so out of the box that they’ll forever change the chitchat between bff’s.
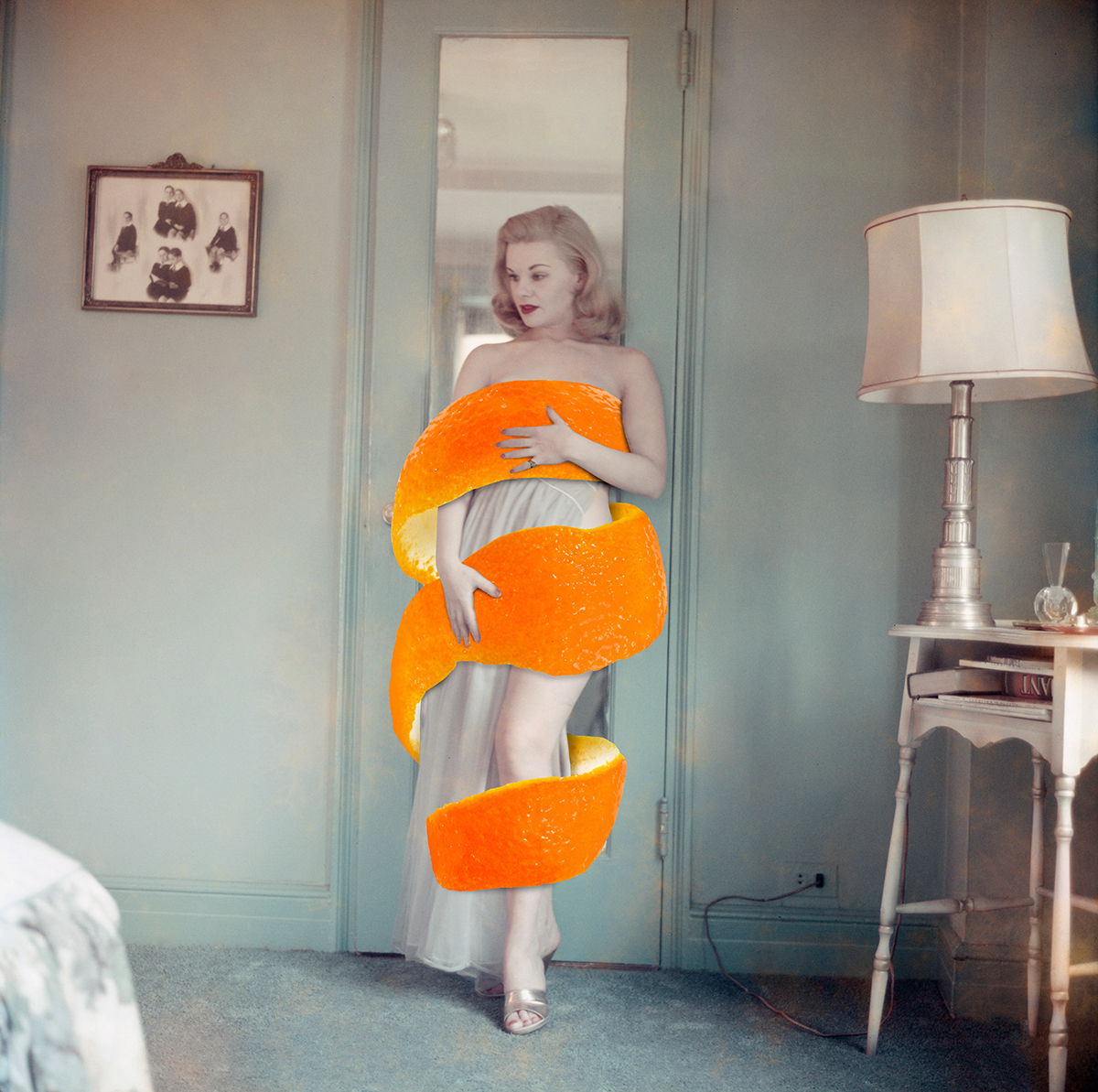
If Sex and the City had been shot in today’s day and age, the dialogue of the fantastic four might have taken on new nuances when it comes to wardrobe references: maybe Carrie’s love for shoes would have taken a vegan route; Charlotte’s denim would have used less water in its production; Miranda’s suits would have been second-hand; and Samantha’s jewelry would have been from a small Soho designer instead of a giant Fifth Avenue brand. If we were to put another decade on top of that, the wardrobe characteristics would be even more revolutionary: fabrics made from food, shoes produced by bacteria that are waste-free, lab-created diamonds… Although they sound like utopic, these options seem to be just the tip of the iceberg of innovations that prove that, when you bring together imagination and resources, creativity happens. Fashion’s concern about sustainability is hardly something new. In fact, more than luxury, massification, trendy or style, the most frequent vocabulary now associated with the industry seems to be exactly that: sustainable. The streamlining of production processes has been focusing on the downsize of resource usages such as water and electric power; the concern with the origin of materials that make each piece is now transparent in both big and small brands, the majority of which substitute the entire collection, little by little, for recycled, organic and of smaller environmental impact versions; and, generally speaking, the big names in Fashion have adopted a policy of environmental responsibility which surpasses the pressure of public opinion – it is necessary. And since need is the mother of invention, what came to be is as needed as it is peculiar. Of course, recycling, reutilizing, and upcycling existent pieces, whether through customization or their transformation into new fabrics, are signs of progress that need to be praised in this mission of closing the production cycle, but there needs to be real imaginative power to be able to look at an ordinary kitchen ingredient and think: “I could wear that”. And it takes high doses of creativity to make it happen.
Like, for example, creating fabrics from foods or natural organisms. One of them, Piñatex, is made from the fibers of pineapple leaves, which means they not only have an organic origin, but they also repurpose scraps, which reduces waste. The fabric, a kind of leather created through a low-environmental-impact process, was imagined by the small leather goods’ specialist, Dr. Carmen Hijosa, who ended up founding the company that patented the fiber, Ananas-Amam. Since we’re bringing fruit to the table, let us also talk about oranges and their derivatives: juices, jams, tarts and sweaters. The Orange Fiber is an Italian company that created a cellulosic fiber with a silky effect that is born from citrines, and their juice, also mixable with silks and cotton to multiply the variety of results. The company has already patented its industrial production and has promised to “rescue” annually more than 700.000 tons of orange peels from the garbage landfills of Italy. And speaking of breakfast classics, maybe it was around that time that the German microbiology student, Anke Domaske, had the idea to use milk, tea and coffee beans for her project Grow your own clothes. Which started as a nonallergenic fabric search for her dad, who was a cancer patient, ended up in the discovery of a fiber now called QMilk – and in the establishment of a company with the same name. The fiber is made out of milk: after separating the protein, the powder is mixed with water to form a paste, then transformed into textiles. The final product, she assures, is as soft as silk and makes leather grow softer with every wear since taking into consideration that milk has various vitamins and minerals, it absorbs and holds hydration. The fiber can also be used in natural cosmetics and organic plastic, besides countless other uses beyond clothing.
Do you feel like there’s no way you can assimilate all this information without a cup of coffee? This Taiwanese couple would have never thought of this fabric without it either: the threads of S.Cafe are the product of the work of Jason Chen, who took his wife advice when she told him, jokingly, that he should put coffee on his clothes so they wouldn’t smell as bad after exercising. Four years and lots of hard work later, a material made out of grinded coffee beans, which usually get thrown out, was born. The final fiber can control odor, it has UV protection elements and dries fast, which makes it perfect for those who love to work out – but not only them. And since we’re talking about exercising, what is most often recommended to athletes? Bananas. A recommendation apparently not connected to clothes, this is if you’re not creatively savvy like the brand Qwstion, which created the first technical fabric made from banana-tree leaves cultivated in the Philippines. Bananatex, as it is called, is covered in natural bee-wax and besides being impermeable, it is long-lasting and biodegradable. Another food that became an Autumn/ Winter favorite is grapes which, by the way, besides wine, can also give us leather. In fact, leather that comes from wine “leftovers”: VegeaTextile is using these disregarded (leather, stalks and seeds) bits that remain from winery production to create vegan leather that is already being used in eco-conscious collections by brands such as H&M. What pairs well with wine? Cheese. But actually, we’re going to talk about chips, which is yet another popular snack: Parblex is a fiber created from potato derivatives, or better yet, waste that comes from the industry connected to potatoes. The company Chip[s] Board wanted to develop a circular philosophy instead of using source materials and, therefore, transforms the leftovers of production of chips (something that doesn’t go through the quality control for nutritional intake), like McCain Foods Limited, in reinforced bioplastic fibers that can be used both in the industry of Fashion and in décor. On the other hand, the enterprise Circular systems looked at all this and thought: why have only one when you can have them all? And then went on to transform six types of harvest wastage into natural fiber products. Hemp seed oil, flaxseed oil, pineapple leaves, banana-tree leaves, cane brandy and rice straws were scraps that now became textiles, creating, as they’ve said themselves, more than 250 million tons of fiber that would have otherwise be turned into waste for the planet. The initiative was at the inception of a clothing company named Agraloop BioFibre, but the raw materials can also be used to create alternative paper packaging, organic fertilizer, biofuel, among others.
But innovations in materials don’t only grow from the soil: the sea has been a crucial source of new textiles for the market, some of them of a kind of “alien” nature, as is the case for fibers created from plastic (Seaqual, for example) and fishing nets (Econyl) taken from the oceans, others take from its fauna and flora to build a biodegradable base for materials. Algiknit is an example of this creativity that is born out of marine organisms since it is made out of this seaweed called kelp. The extrusion process transforms the mixture of biopolymers (polymers produced by living organisms) in a thread of marine origins that can then be woven, or 3D printed in order to minimize waste. The final knit is biodegradable and can be tinted with natural pigments. The usage of seaweed can also be combined with other materials – like Seacell, made from Lyocell (a natural fiber created from cellulose) and seaweed. Perfect for underwear and sportswear pieces, it is a long-lasting fabric that absorbs sweat 50% quicker than cotton. Besides, thanks to the mineral substances in its composition, such as calcium or vitamin A, it also has positive effects on the skin. This high concentration of vitamins and minerals that are found in seaweed also makes it a good candidate to be used on supplements and cosmetic products. What should we take from this analysis? That the food industry is more connected to Fashion than we thought, yes. And that one of the central points of these alternatives, not mentioning the most primary one – to think outside the box – is to use resources that would otherwise be considered garbage. More than looking in fruits, foods, and in the ocean for textile alternatives that will reduce how much we rely on traditional raw materials, the point is to minimize waste. And the advances in this department have been so impactful that there are options already reaching the zero-waste benchmark – with a little help from our friends, the bacteria.
Theane Shciros, a teacher at the Fashion Institute of Technology and a scientific investigator at Columbia University, NYC, is a specialist in biofabrics (meaning, the development of textiles in a laboratory) and joined forces, last year, with the designer duo from the brand Public School, Dao-Yi Chow and Maxwell Osborne, to “grow” a pair of sneakers from fermented bacteria. The sneakers, with a diminutive carbon footprint, also have a zero-waste impact, because they’re produced on a mold that doesn’t generate any excess fabric. The creators’ idea was to target a customer base that is ever more demanding about the origin and history of their products, at the same time as they are knocking down the barriers at the service of sustainable Fashion: “We have mechanical and chemical properties, as well as the biodegradable organism – this gathers all the variables needed to create an impact in the industry”, Schiros affirmed, at the time, to the WWD website, underlying the capacity of such a discovery has to resolve existential threats bound to the production chain for clothing. The shoes are composed of nanofibers of cellulose created by bacteria whose final imprint is similar to the one of leather. According to Schiros and her team’s analysis, the environmental impact of this microbial leather is 100 times smaller than the one of vegan leather, which is made out of plastic. The project was created within the scope of the One X One initiative, an incubator program proposed by Swarovski and Slow Factory with the support of the United Nations – and it wasn’t the only one worthy of mention. The American creator Phillip Lim also worked closely with the industrial designer Charlotte McCurdy to develop sequins that would be made out of seaweed instead of plastic, demonstrating that there are infinite alternatives to the circuit of production of Fashion, especially science, design and creativity work together, side by side. A few years before, in 2017, Stella McCartney also joined Bol Threads to conceive a spider-silk dress, a laboratory-created fiber – North Face did the same, deriving it in a material called Spiber, which resulted in a jacket for the brand. “This idea of being able to experiment at an initial level and understand how we can produce in scale is the biggest opportunity for the industry”, Chow, from Public School, highlights. “The goal is to only do what is needed. No one really needs another pair of sneakers”, he states.
The biggest obstacle is precisely that: scale production, being that, at this moment, scaling doesn’t need to be – and shouldn’t be – a synonym of massification, which has a tendency to be wasteful, nor should it feed into the unhinged consumerism at a time where the motto is to consume less and better. The goal is to create a chain of production that is as close as possible to the level of demand, practicing accessible enough prices to turn these advances into a reality of daily life and not just hope in a sample tube. But, as history has come to prove, technological advances almost always happen overnight: ten years in the XXI century for technology is abysmally different than the same period in the XX century. Especially, if creativity has anything to say about it. Who would have thought to use flora for clothing? If Adam and Eve did, then it’s not creative. That was their last resort. Creativity means applying the synergies of the natural work and the industrial world together in a symbiosis that is not only sustainable from the Earth’s point of view, but also for humanity, who no longer wants to forfeit the comfort and advances it conquered throughout the centuries. Which addresses just as much the needs of the public as it of the planet. Though imagination remains boundaryless. I would know because I took notes for this article with a pen made out of discarded coffee capsules while wearing a sweater made of plastic bottles retrieved from the ocean. Made in the future.
Translated from the original article from Vogue Portugal's Creativity issue, published in March 2021.
Relacionados
.jpg)
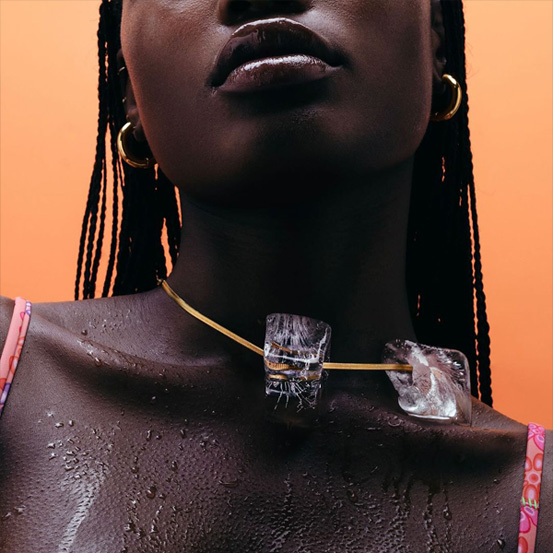
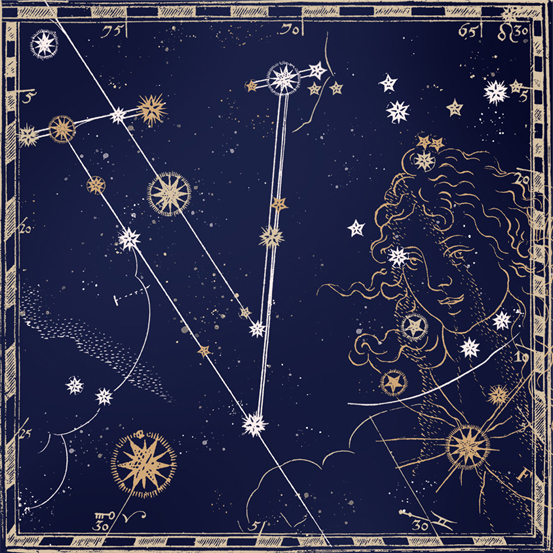
O que lhe reservam os astros para a semana de 26 de agosto a 1 de setembro
26 Aug 2025